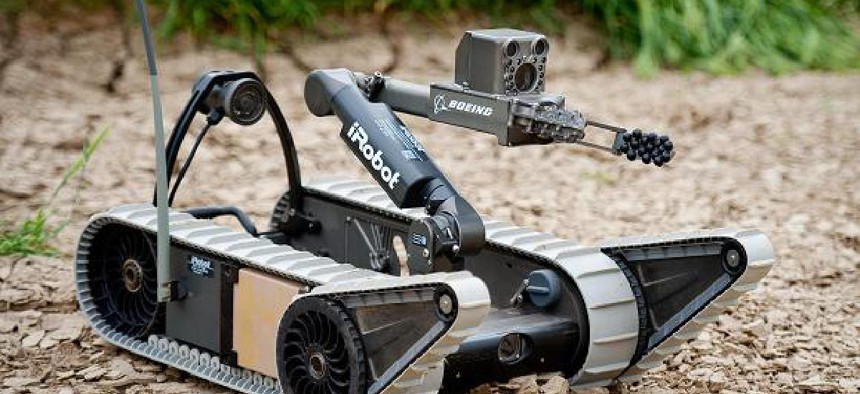
New kits allow soldiers to diffuse IEDs and innovate with 3D printing in combat
Software catalog helps find the specs on parts that need replacing.
When an IED diffusing robot loses a tread or a nitrogen purge pump handle breaks, soldiers in the field are usually left with few options and a long wait for a replacement part. However, a new portable Rapid Fabrication (R-FAB) kit with 3D printing capabilities could be about to change that.
“R-FAB allows rapid repair or soldier innovation at the point of need,” said Capt. Jeremy Pinson, Additive Manufacturing Lead for the Army’s Combined Arms Support Command.
The R-FAB expeditionary kits will be three dimensional and use additive manufacturing, a method of construction that includes 3D printing, according to the Army. Additive manufacturing means that a tool or part is constructed starting with nothing and layering material to form a desired shape, as opposed to methods such as carving or drilling, which remove material to achieve the right shape.
"R-FAB allows soldiers and leaders to increase their readiness by making authorized replacement parts,” said Capt. Pinson. “For example, a robot tread could be printed. That tread may not be as good as an original equipment manufacturer part, but the part will get the soldier through the next mission,” explained Capt. Pinson.
In terms of rapid repair capability, the infield R-FAB kits will come equipped with the necessary gear and software for the construction of any tools and parts, according to the Army. It will also have a software database of design blueprints, known as Raptor.
The Raptor software catalog is designed to facilitate the process of finding and printing the right part for soldiers in high-intensity situations. The user need not even know the exact part that needs replacement, reported a U.S. Army Training and Doctrine Command (TRADOC) press release. As long as the right system is chosen, the screen will display pictures of commonly broken parts to choose from. One click, and the part will begin printing.
“Sometimes they have a hard time getting…parts fielded forward, so we are telling soldiers to make it, to get through the mission,” said James L. Zunino, Materials Engineer with the Armament Research Development and Engineering Center. “You know that you have a PackBot, and you can click on the PackBot picture… and it will bring up all the components you can print,” he explained.
The other aspect of the new R-FAB capability, as described by Capt. Pinson, is innovation.
“It’s for things the soldiers could modify for themselves, you could do mass customization, you could print in the field…you can actually tailor a weapon for how the soldier wants to use and operate it,” explained Zunino.
Technological needs for soldiers in the field can be constantly evolving, and with a portable manufacturing kit and software, soldiers can construct new tools or tweak existing design plans, according to TRADOC.
For example, CW2 Ron Billingslea, an Allied Tradesman with the 47th Brigade Support Battalion, described how soldiers used 3D printing to create a tool for opening 55-gallon drums that had refused to budge for any of the existing tools they had tried.
However, both Zunino and Capt. Pinson emphasize that the R-FAB products are not intended to replace traditionally manufactured parts. Instead, they are intended to support missions and operations during the time lapse between a part breaking and the arrival of the manufacturer replacement.
The 3D printing technology is partially made up of commercial-off-the-shelf technology, and is meant for deployment as close to the point of need as possible, according to the Army. It will also be available to some maintenance units.
“The main objective is to meet Army readiness goals, which is a directive of the Secretary of the Army. Filling the gap until spare parts are delivered will greatly increase the operational tempo of the warfighter," said Zunino.