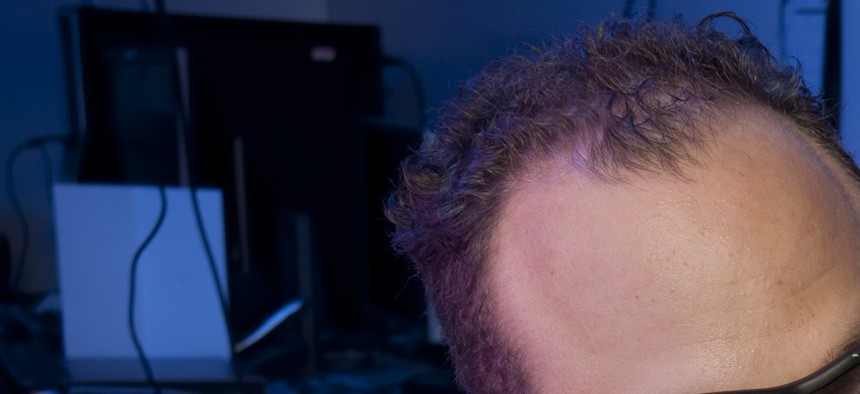
A 3D Printer at the Edgewood Chemical and Biological Center U.S. Army
Why Is the Pentagon Dragging Its Feet on 3D Printing?
Troops in Afghanistan are testing 3D printers on the battlefield, but the military's acquisition process is getting in their way. By Kyle Chayka
In August 2010, Navy Lt. Cmdr. Michael Llenza was perched in his jet ready to return to base in Bagram, Afghanistan, when a valve on the plane broke. “I was stuck,” he recalled. “The whole squadron was taking off and I’m sitting there.” The pilot would have to wait weeks for a replacement part to be shipped from a carrier in the Indian Ocean. A thought came to Llenza: “Wouldn’t it be great if I could walk back into the hangar and print out a part?”
What Llenza had in mind was three-dimensional printing, a burgeoning technology that allows its users to transform digital models into physical objects. Also called additive manufacturing, 3D printing works by extruding materials, including plastic, latex, and ceramic, through a printer nozzle layer-upon-layer until the object is fully shaped, like an inkjet printer with a vertical as well as horizontal axis. The process could have created a new valve for the lieutenant commander in a matter of hours rather than weeks, and for much less than cost of international shipping.
Llenza and others in the Army and Navy are calling for a comprehensive policy that could solve some of 3D printing’s inherent difficulties and take full advantage of its revolutionary potential. Though 3D printing is successfully being adopted in the U.S. military, the Defense Department “does not have a clear strategy” in approaching the technology, Llenza critiqued during his study of printing’s military applications as a 2013 fellow at the Atlantic Council's Brent Scowcroft Center on International Security.
Where 3D printing is being employed, it’s already making troops’ lives easier. The Army is launching “expeditionary labs,” self-contained spaces designed by its Rapid Equipping Force that hold manufacturing equipment including 3D printers and Computer Numerical Control machines. The first two labs were deployed in Afghanistan last year, and the third is being completed this summer. The labs allow troops to collaborate closely with engineers to quickly fix problems on the ground.
Former REF Director Peter Newell cites the example of MRAPS in Afghanistan. The valve stem on the vehicles’ front tires was often exposed to rocky terrain, causing them to break. Soldiers brought the problem to an expeditionary lab, tested various iterations of a valve cover, and shipped a model data package for the perfected design back to the U.S., where the parts were professionally manufactured—a “30-day discussion rather than a multi-year process,” Newell said.
The Edgewood Chemical and Biological Center in Maryland, part of the Army’s Research, Development and Engineering Command, has been at the forefront of 3D printing since the 1990s, using it to create prototypes for testing, explained Rick Moore, ECBC’s Branch Chief of Rapid Technologies and Inspection. Using printers, Moore’s team can quickly and inexpensively “go through iterations of designs until we get it exactly the way we want it, then invest in larger scale manufacturing,” he said.
Through rapid prototyping, Moore has developed projects like battery storage for night-vision helmets and specialty tools for unmanned vehicles. But rather than designing products back home and shipping them to troops, Moore’s ultimate goal is to arm the soldiers with the same manufacturing capabilities he has. Certifying the technology and deploying it on a large scale, however, may require fundamental changes in how the military approaches technology.
While companies like GE and Boeing are already printing out integral elements of their machines and vehicles, the military’s certification process blocks them from doing the same, according to Michael Llenza. There’s no formal test in place for the unorthodox materials that printers use, and the results are hard to standardize in soldiers’ disparate environments. “We have to revamp the whole acquisition process,” he argued.
Because 3D printing can create a physical replica of any digital file, “the back-end data” for a part “is more important than the widget itself,” Lt. Benjamin Kohlmann, a Naval Innovations and Concepts officer, said. This means that in order to legally print parts, the military will also have to buy the replication rights to each module. That, or allow troops to develop their own, novel tools that exist outside of traditional copyright.
After his 2012 essay calling for more “disruptive thinkers” in the military, Kohlmann has become a poster child for defense innovation. In the DoD’s “incredibly siloed and bureaucratic system, it takes decades to bring normal technologies to front lines,” he said. As part of the Navy’s Rapid Innovation Cell (CRIC), a core group of 15 young officers exploring new technology, Kohlmann is hoping to change that, focusing first on 3D printing.
Kohlmann is overseeing an initial printer trial at Navy Warfare Development Command in Norfolk, Virginia. In the next year, he hopes to install printers on a carrier to help with medical instruments and prosthetics, but also “open it up to the crew at large” to see what they produce—he suggests non-mission critical objects like gaskets and gear clips, avoiding certification problems while fulfilling a vital, everyday need. Kohlmann’s ultimate goal is a database of digital models for parts that can be safely 3D printed. “This is a test bed to see what will happen,” he said.
Enabling experimentation is one of the chief strengths of 3D printing, particularly where quick solutions are the priority. “The forward edge of the battlefield is where the true advantage is,” REF’s Peter Newell said. Such was the case for the MRAPs as well as other cases like a 3D-printed flashlight guard that kept the bulb from going on, revealing soldiers’ positions.
Yet the transience of the battlefield presents another obstacle for 3D printing. “Just as someone is getting comfortable with it all of a sudden they’re being redeployed,” Rick Moore pointed out. The solution is to create the conditions for experimentation and innovation throughout the military, making 3D printing part of a dialogue around equipment evolving from the soldier up rather than higher echelons down, Kohlmann recommended.
Without that creative environment, the military is in danger of falling behind commercial industry and failing to embrace a technology that is already saving lives, money, and time. “We have to be ready to integrate systems when they come out,” Kohlmann said. “We don’t want to play catch up.”
Kyle Chayka is a freelance writer living in Brooklyn. He reports on technology and culture for Pacific Standard, New York Observer, and Animal New York, tackling 3D-printed guns and legal marijuana start-ups, among other unorthodox subjects.