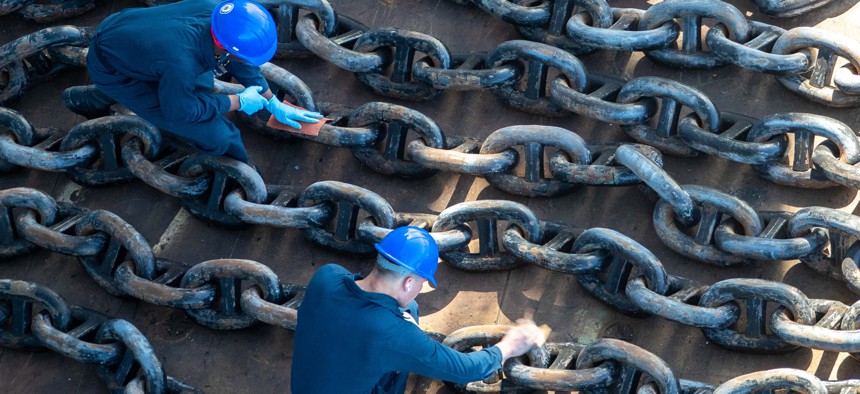
Navy Seamen Kevoy Gordon, left, and Andrew Crickard sand and prepare the USS Tripoli’s anchor chain for painting during a maintenance availability in San Diego, April 20, 2023. U.S. Navy / Petty Officer 1st Class Danian C. Douglas
How the Navy is using deployed ships to improve maintenance
The goal is to keep ships at sea and those in queue up to date, the service’s surface warfare director said.
The Navy is using data from warships deployed in the Red Sea to improve its predictive maintenance and modernization efforts.
“We have opportunities to leverage real-world data given what the team is doing in the Red Sea right now,” Rear Adm. Fred Pyle, director for the surface warfare division in the office of the chief of naval operations, said Thursday at Govini’s Defense Software and Data Summit in Washington.
The Navy’s Surface and Mine Warfare Development Center manages and analyzes that data, then pushes it back to the deployed fleet.
“We take the lessons learned, we feed that back to the ships that are in theater to make sure they have the most current tactics. And at the same time, we're feeding into the next deployers so as they work up and they certify, they have that information as well,” Pyle said.
The Navy is also leaning on its software factory at land-based sites, he said, such as Wallops Island, Va., to reduce maintenance risks so that “whatever they're gonna deploy onto an afloat platform has at least been tested on a like system ashore.”
The Navy has been broadening its predictive maintenance efforts, weaving in automation, robotics and artificial intelligence. But the service still struggles to manage the data it has.
“We have 73 destroyers in the fleet today. We've been building this program for four years; we've been modernizing these ships for over three decades. So there's a ton of data out there,” Pyle said. “But the question is, do we have it in the right format so we can actually leverage that data? And that's something we're working on.”
One of the challenges is scheduling work far enough in advance—about 120 days— to give contractors time to make sure they have labor and parts ready for when a ship comes into drydock. That monthslong lag is partly due to the need for ship checks, a historically manual process the Navy wants to modernize.
“We're working to automate that process so we can leverage that data from four-plus decades and get to a more predictive…work package,” Pyle said. And “reducing the number of days in delayed maintenance.”
More automation could also prevent major surprise repairs, which can cause significant delays.
“That's an area where we struggle,” Pyle said. To fix that, the Navy must define the work package and use data to “make sure we understand the condition of the ship as it goes in.”
“Ships are coming into drydock and they need…to be scanned, you need to know where the defects are, what the problems are. Then you have to put it against the budget, to put it against the timeline, create a repair. So doing that in an automated fashion gets the ship in the ocean faster and increases battle readiness” and ultimately efficiency, Bruno Pontes Soares Rocha, chief operating officer for Gecko Robotics, said at the conference.
Gecko Robotics is currently using its predictive maintenance technology—a combination of robots and AI—to inspect the Navy’s Columbia-class nuclear submarines.
“But the problem is, we have parts from hundreds of suppliers that need to fit together. And there is a lengthy process” to make sure “they're actually going to fit,” he said. “There's a lot there, we're starting to see orders of magnitude gains in efficiency, but it's just the tip of the iceberg.”