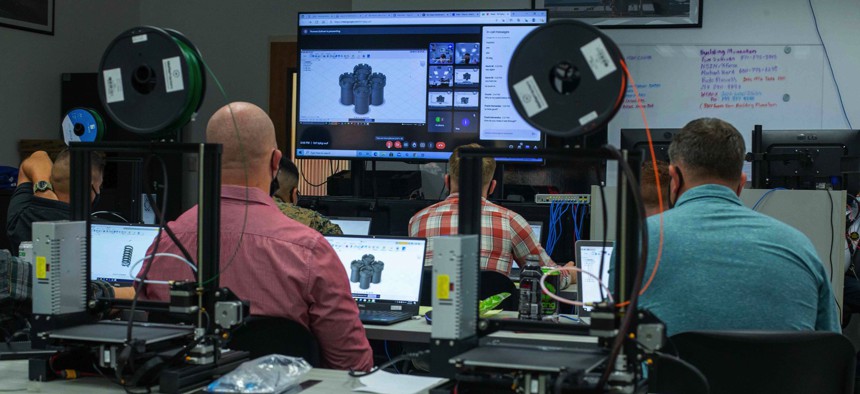
U.S. Marines with I Marine Expeditionary Force Information Group, learn how to 3D print a castle during the Building Momentum Innovation Bootcamp at Camp Pendleton, California, Sept. 27, 2021. U.S. Marine Corps / Cpl. Aidan Hekker
Marine Makers: How I MEF Troops Are Putting 3D Printers to Work
From generator covers to car parts, a Marine describes how additive manufacturing helps his unit get on with its mission.
SAN DIEGO—When a door handle broke on a multi-ton vehicle, the group of Marines had two choices: drive 40 minutes across Camp Pendleton to get a replacement part with the door flapping open—or make it themselves right there.
Lance Cpl. Maximilian Pohlmann, who leads a team of three charged with running 3D printers for I Marine Expeditionary Force’s 9th Communication Battalion, chose the latter.
Pohlmann can print out vital parts on the go using a 3D printer as part of a project that can save the Corps time and money.
“At first, when this project started out, it was just a 3D printer in a box,” said Pohlmann.
Now, the printers are fully operational and have been used to recreate vehicle door handles and components for satellite communications equipment.
Pohlmann is most proud of printing a case for a satcom component that was no longer made by the manufacturer.
“You can still get all the parts, the internal components, of the combiner divider. And so we can just manufacture the entire thing in house for $500 versus the $1,600 you'd have to spend to get a new one,” he told Defense One on the sidelines of the WEST conference here.
“So if anybody comes to me with an idea, I can go ahead and move on it. And then, of course, if it's not a mission-critical system, I have full rein to go and try out my parts and verify that they work before I send them up to the program office for approval.”
The battalion's additive manufacturing project is largely focused on maintenance, but there’s potential for more. Here’s how Pohlmann sees it:
You're in charge of this 3D-printing machine. What do you use it for?
We use thermoplastic filaments in order to recreate broken parts, replacements, innovate new designs, make things 3D-printable that were not 3D-printable before in order to replace and improve the quality of life within the battalion.
Name a time when using it was really important.
There was a handle that broke off of one of the seven-tons [vehicles] while we were out on the field op. It's a pretty big truck. And one of the door handles snapped off of this seven-ton and the door would not remain closed unless we got a new door handle in. And getting a new door handle would have required us to go all the way back to the battalion, pick up a spare there from what we had, and then drive it all the way back out.
But instead we just took the old one that was broken, we designed something equivalent, and then printed it out in a matter of 45 minutes and had it on the vehicle ready to go and it was functioning.
Do you just scan the broken part?
I wish we had a 3D scanner, no. Usually what I'll do is I will take the best reference frame that I can. If it's a door handle, for example, I take the door handle off the other side if they're the same, and I'll use micrometers to measure out distances, circumferences, everything I can in order to give myself the best 3D vision of the part itself. Take notes on all of the measurements that I make and then use a program such as SolidWorks or Fusion 360 in order to CAD out the design and then convert it to a stereolithography file and send it to the slicer of the 3D printer, which then formats it into Gcode and then puts out plastic and it prints.
How long does that take?
Depending on the complexity of the part and the size of the print that it ends up needing to be? I've had the whole process—turnaround time can take anywhere from 45 minutes to over five days straight worth of printing.
What would take a week to print?
It was the cover for a generator, the emergency cover panel for that. The lock for the original panel had broken and it needed to be replaced because without the cover panel, there's water that can get inside the generator if it rains, which will absolutely destroy that generator.
Due to the sheer size of the panel and with the print bed that I had available to me, it ended up being a four-part print with each part taking over around 26 hours.
Did you always want to do this?
No, not at all. I’m a [satellite communications repair technician]. We had 3D printers just sitting around. They were like, “Oh, hey, this is for maintenance; use them.” Saw a buddy of mine was working with them and was like, “Hey, can you teach me this?”
My father-in-law had sent me a 3D printer in the mail that he couldn't use—it was a wedding present. So I brought it into the shop one day.
And so then I learned how to 3D-print. I got my own 3D printer and then I started working more with the Marine Corps ones as well. And I've just been doing it ever since.
What’s next? Training anyone?
Oh, yeah. Anytime anybody shows any interest, people will come into my workspace and they're like, “Hey, 3D printing That's dope as hell; let me get in on that.” Then I'll pull them aside, if they're serious, teach them how to CAD something and then we'll use their CAD and throw it on one of my printers so they can physically see their own work. It really helps in the learning process.
What would make your job easier?
I don't personally have the equipment [required to bind and sinter metal] in-house. So I don't do any actual metal printing in house. I print the metal and then I send it out. I don’t metal print in the field.
I wish I could. That would be amazing. Like, say, if the battalion bought me that equipment and I could take it with me. I would love to do that. That would be great. But in the field, I have thermoplastics and I make do with what I can.